Digitize Work Instructions
Digitizing procedures is a major part of a paperless factory. But it must also enable employees to access information more quickly and efficiently.
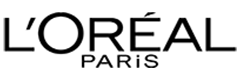

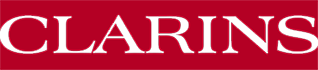

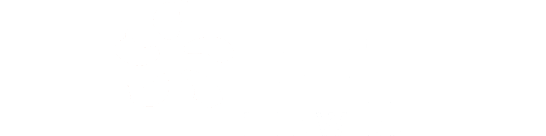
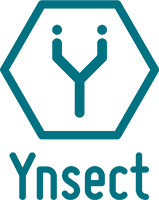

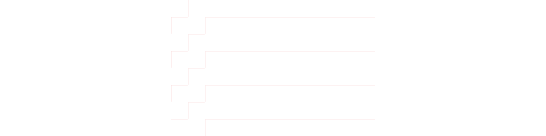
.png?width=245&height=214&name=Frame%201312%20(1).png)
.png?width=245&height=214&name=Frame%201448%20(1).png)
.png?width=245&height=214&name=Frame%201449%20(1).png)
.png?width=245&height=214&name=Frame%201450%20(1).png)
Presentation
Centralize Access to Critical Operational Knowledge and Manage Work Instructions
It's easy to create and distribute standards across different shifts and plants. Visual, one-point lessons in a Training Within Industry (TWI) format complement written SOPs, making it easier for workers to comprehend and remember the instructions.
Simplify the management of your work instructions:
- Create and distribute standards easily across different shifts and plants
- Improve employee access to critical information
- Reduce production deviations and foster a culture of standardization
- Decrease the effort required for documentation creation and management
- Enhance understanding and retention of essential information
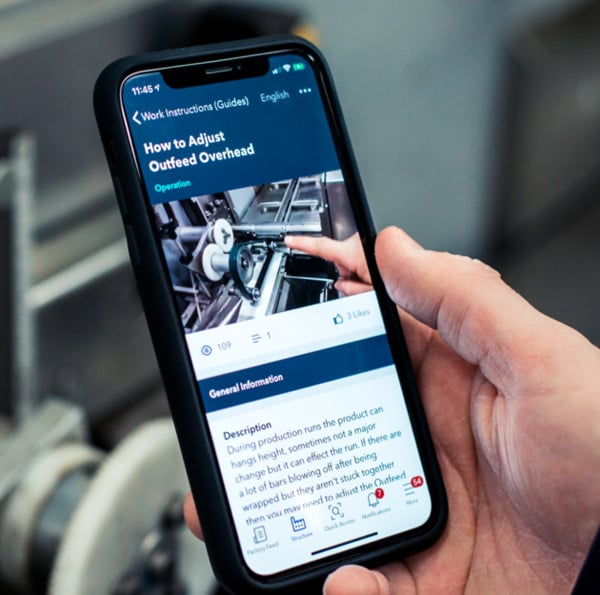
Your Challenges and Stakes
Your plant's knowledge base
A centralized plant knowledge base facilitates knowledge transfer between teams by consolidating best practices, lessons learned and standardized procedures. This enables employees to quickly access relevant information to solve problems and suggest improvements. It also facilitates staff training by providing centralized access to training resources and facilitating the integration of new employees. Finally, by keeping track of knowledge and practices even in the event of staff turnover, it ensures continuity of operations and the preservation of corporate know-how.
Standardize your work instructions
In a factory, process uniformity for identical equipment is crucial to guarantee consistency, reliability and production quality. By having identical release processes, errors are minimized, maintenance is simplified and staff training is more effective. It also optimizes performance and facilitates compliance with safety and regulatory compliance standards. Ultimately, this harmonization of processes helps to maximize operational efficiency and ensure consistent, high-quality production.
Standards and audit compliance
A well-documented knowledge base, with version management and access to a full version history, reinforces compliance with standards and factory audits by providing clear documentation, traceability of changes and easy access to relevant information. This helps to demonstrate to regulatory authorities and customers that plant processes comply with current requirements and guarantee the quality and safety of manufactured products.
prev
next
Main Features of AVEVA to Digitize Your Procedures
Accessible and multiplatform
The solution needs to be accessible from a variety of devices, such as desktops, tablets and smartphones, to enable flexible use in the field and in the office. Users must be able to find the information they are looking for quickly and efficiently.
Version management
It is crucial to be able to manage the different versions of work instructions efficiently, ensuring their traceability and enabling users to consult the relevant versions. Whether for auditing purposes, or simply to keep track of procedures, it's important to have a simple, clear version history.
Approval matrix
By integrating an approval matrix into their document management system, companies can strengthen their compliance with regulatory and industry standards, while improving the efficiency of their document validation processes. It is important to be able to configure customized approval workflows, determining who must approve each type of document, and in what order.
Advanced search
Advanced search functions, such as keyword, category or tag searches, are needed to enable users to find relevant work instructions quickly. Indeed, digitizing procedures should make it possible to access the right instructions more quickly.
Procedures and programs
The use of digitized instructions aligned with the current program at equipment level offers an effective means of optimizing manufacturing processes, while ensuring rigorous compliance and enhanced operational efficiency. For example, at MES level, the instruction can be displayed automatically once the program to be launched has been selected.
Which AVEVA software meets your needs for standardizing work instructions?
AVEVA Teamwork
AVEVA Teamwork is a platform that addresses the factory's needs for knowledge, training, communication, and tracking of your daily meetings.
Connected worker
They Talk About Us
Get a demo
Customer Testimonials
“AVEVA Teamwork has enabled us to gather field information, understand our dysfunctions and analyze them, to implement the necessary actions to correct discrepancies, capitalize and provide the same information to the entire team.”
Eddy PAULY
Production Manager
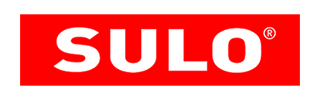
Go further in workforce skills & operational knowledge management with AVEVA software.
Factory training
Troubleshooting and problem solving
Industrial systems are becoming increasingly complex, so effective training is becoming essential. Find out how AVEVA products can help you train your employees.
Learn more

In the industrial environment, one of the major challenges is to minimize machine downtime as much as possible through rapid diagnosis and problem solving.
Learn more
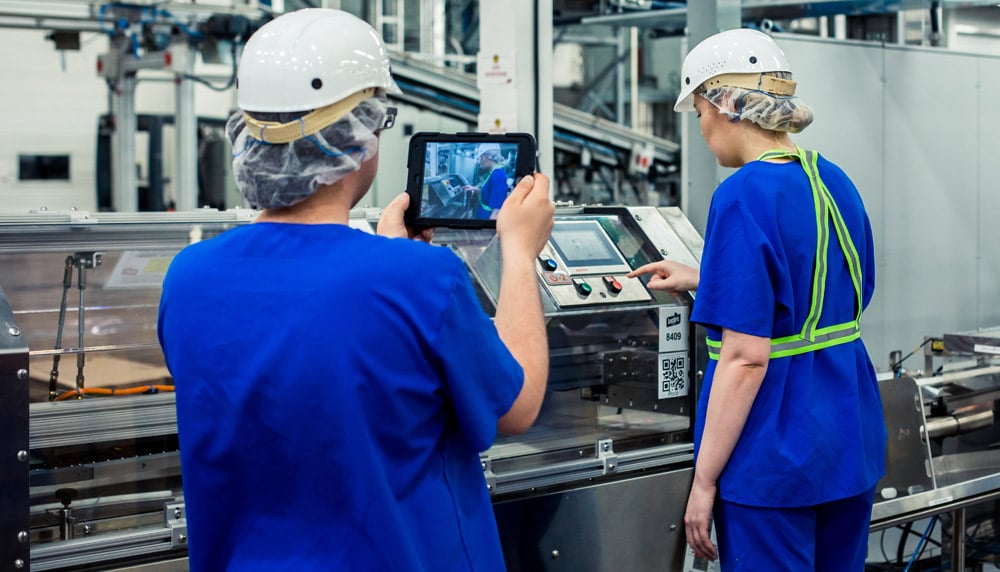