Advanced Planning and Scheduling PlanetTogether (APS)
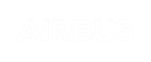
.png?width=220&height=89&name=Logo_Factory_RVB-03%201%20(2).png)
.png?width=220&height=89&name=Logo_Factory_RVB-03%201%20(2).png)
.png?width=220&height=89&name=Logo_Factory_RVB-03%201%20(2).png)
.png?width=220&height=89&name=Logo_Factory_RVB-03%201%20(2).png)
.png?width=220&height=89&name=Logo_Factory_RVB-03%201%20(2).png)
.png?width=220&height=89&name=Logo_Factory_RVB-03%201%20(2).png)
.png?width=220&height=89&name=Logo_Factory_RVB-03%201%20(2).png)
.png?width=220&height=89&name=Logo_Factory_RVB-03%201%20(2).png)
.png?width=220&height=89&name=Logo_Factory_RVB-03%201%20(2).png)
.png?width=220&height=89&name=Logo_Factory_RVB-03%201%20(2).png)
.png?width=220&height=89&name=Logo_Factory_RVB-03%201%20(2).png)
.png?width=220&height=89&name=Logo_Factory_RVB-03%201%20(2).png)
.png?width=245&height=214&name=Frame%201312%20(1).png)
.png?width=245&height=214&name=Frame%201448%20(1).png)
.png?width=245&height=214&name=Frame%201449%20(1).png)
.png?width=245&height=214&name=Frame%201450%20(1).png)
Planning and scheduling automation
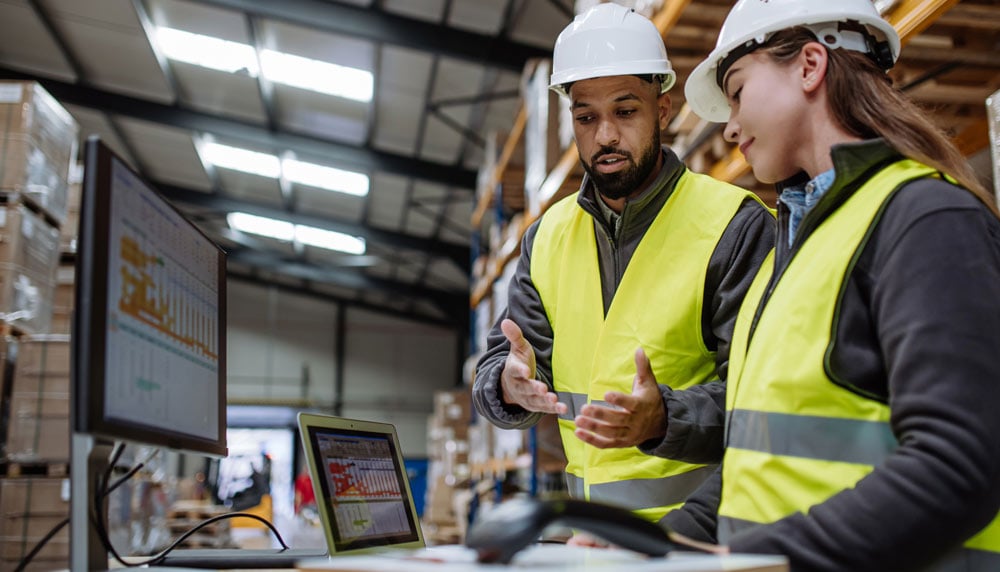
What makes Advanced Planning and Scheduling PlanetTogether unique for planners?
Provide complete visibility into your plant’s planning so your teams can react quickly to unforeseen events, adjust schedules, and optimize the allocation of resources and your teams. This flexibility facilitates scenario simulation, continuous process improvement, and guarantees better productivity, by ensuring controlled deadlines and proactive adaptation to changes.
Top Advanced Planning and Scheduling PlanetTogether features for developers
Also, views can be modified according to users preferences to show them the most useful data and information to them. Their settings are all stored as part of their Workspace Profile which can be shared with other users, if desired.
Users may also share (export) their Profiles so that other users may import them. Profiles can be exported to a shared collection that gets stored within the Workspace, or exported to a file that can be moved from one Workspace to another.
The PlanetTogether Report Designer is used to create and modify Reports that can be loaded into PlanetTogether.
It allows you to create custom reports, with access to the entire dataset of PlanetTogether and the possibility to get data from other sources if you want to cross your data to have complet reports.
Discover Certified AVEVA Integrators
The questions you have about PlanetTogether APS
The PlanetTogether Advanced Planning and Scheduling (APS) system offers rapid and adaptable capacity planning, scheduling for production, and MRP (material requirements planning), integrating seamlessly with your current ERP system.
- Boost sales through reduced production lead times.
- Decrease stock levels by synchronizing manufacturing processes with actual demand.
- Lower per-unit expenses through more efficient manufacturing cycles.
- Enhance decision-making with insights into capacity, scenario planning, and analytics.
Planning and scheduling within a factory are essential pillars of production management, aligning productive processes with the company's objectives while maximizing efficiency and profitability. Production planning focuses on determining the quantities of products to manufacture, the timelines for completion, and the necessary resources, taking into account capacity constraints and market requirements. It spans several temporal horizons: strategic for the long term, tactical for the medium term, and operational for the short term, to adjust production plans to demand fluctuations and external environment contingencies.
Scheduling, on the other hand, comes after planning. It involves the concrete organization of production on the ground. This means defining the precise order of manufacturing operations, selecting equipment, and assigning personnel to various tasks, all while respecting time and quality constraints. Scheduling aims to optimize the use of available resources (machines, raw materials, labor) to achieve production objectives efficiently, thus minimizing waiting times, intermediate stocks, and production costs.
In summary, planning and scheduling are two complementary processes that together enable dynamic and responsive management of a factory's production activities. They contribute to achieving the company's objectives in terms of deadlines, costs, quality, and customer satisfaction, by continuously adapting production operations to the changing market conditions and internal requirements of the company.
PlanetTogether licenses are available in "Perpetual" mode or "Subscription" mode.
It also offers 2
PlanetTogether can connect to other systems through SQL procedures. As long as it is possible to access the source data of your other system through this procedure, this will be possible.
Complementary products
AVEVA MES Operations
MES Software
AVEVA MES Performance
MES Software